Porosity in Welding: Identifying Common Issues and Implementing Best Practices for Prevention
Porosity in welding is a pervasive concern that often goes undetected till it creates considerable problems with the integrity of welds. This usual flaw can jeopardize the toughness and longevity of welded structures, posturing security threats and bring about expensive rework. By recognizing the source of porosity and applying efficient avoidance methods, welders can considerably boost the high quality and integrity of their welds. In this discussion, we will certainly discover the essential factors contributing to porosity development, examine its harmful impacts on weld efficiency, and discuss the best methods that can be embraced to decrease porosity occurrence in welding processes.
Typical Reasons of Porosity
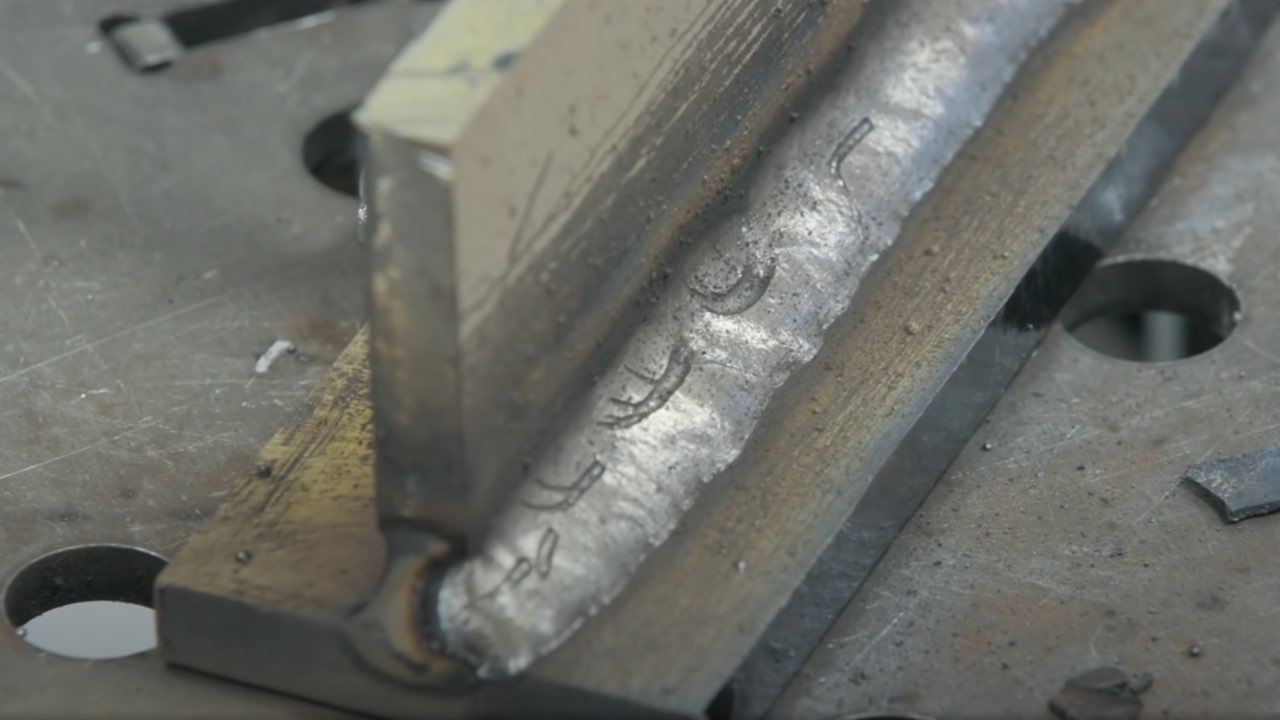
Utilizing filthy or wet filler materials can introduce contaminations into the weld, adding to porosity concerns. To mitigate these typical causes of porosity, extensive cleansing of base metals, appropriate protecting gas choice, and adherence to optimum welding specifications are important techniques in achieving high-quality, porosity-free welds.
Influence of Porosity on Weld Quality

The existence of porosity in welding can substantially endanger the structural integrity and mechanical residential or commercial properties of bonded joints. Porosity develops gaps within the weld steel, weakening its total strength and load-bearing capacity. These voids serve as anxiety concentration points, making the weld more susceptible to splitting and failing under applied lots. Furthermore, porosity can minimize the weld's resistance to corrosion and various other ecological elements, additionally decreasing its longevity and efficiency.
One of the key effects of porosity is a decrease in the weld's ductility and durability. Welds with high porosity degrees often tend to exhibit reduced impact stamina and reduced capacity to deform plastically prior to fracturing. This can be particularly concerning in applications where the bonded components undergo dynamic or cyclic loading problems. Furthermore, porosity can hamper the weld's ability to successfully send forces, causing premature weld failure and possible safety risks in critical structures.
Ideal Practices for Porosity Avoidance
To enhance the structural integrity and high quality of welded joints, what specific actions can be carried out to reduce the event of porosity throughout the welding procedure? Porosity avoidance in welding is crucial to ensure the integrity and strength of the final weld. One effective practice is correct cleansing of the base metal, getting rid of any type of contaminants such as corrosion, oil, paint, or moisture that can result in gas entrapment. Ensuring that the welding tools remains in excellent problem, with clean consumables and suitable gas circulation rates, can additionally substantially minimize porosity. Furthermore, preserving a steady arc and controlling the welding parameters, such as voltage, existing, and take a trip speed, helps create a regular weld pool that decreases the you could try here risk of gas entrapment. Making use of the proper welding strategy for the certain material being welded, such as readjusting the welding angle and weapon setting, can better avoid porosity. Normal evaluation of welds and prompt remediation of any type of concerns recognized during the welding process are crucial methods to stop porosity and produce high-grade welds.
Significance of Correct Welding Strategies
Carrying out proper welding strategies is vital in guaranteeing the architectural stability and quality of bonded joints, building upon the structure of reliable porosity avoidance procedures. Extreme warm can webpage lead to enhanced porosity due to the entrapment of gases in the weld swimming pool. Additionally, making use of the suitable welding criteria, such as voltage, present, and take a trip speed, is critical for accomplishing audio welds with marginal porosity.
Moreover, the option of welding process, whether it you can try these out be MIG, TIG, or stick welding, should straighten with the particular needs of the project to make sure optimum results. Appropriate cleansing and preparation of the base metal, in addition to choosing the right filler product, are likewise essential elements of skillful welding techniques. By sticking to these ideal practices, welders can lessen the threat of porosity formation and create high-grade, structurally sound welds.

Testing and Quality Assurance Steps
Quality assurance measures play a critical role in validating the stability and integrity of bonded joints. Testing procedures are important to spot and prevent porosity in welding, making sure the stamina and durability of the end product. Non-destructive testing techniques such as ultrasonic screening, radiographic screening, and aesthetic inspection are typically utilized to determine prospective problems like porosity. These strategies permit the analysis of weld high quality without endangering the stability of the joint. What is Porosity.
Carrying out pre-weld and post-weld assessments is also critical in keeping high quality control requirements. Pre-weld inspections entail confirming the materials, tools settings, and cleanliness of the workspace to avoid contamination. Post-weld inspections, on the various other hand, examine the final weld for any kind of problems, including porosity, and verify that it meets defined requirements. Executing a thorough quality assurance plan that consists of thorough screening procedures and evaluations is vital to reducing porosity problems and making sure the overall high quality of bonded joints.
Conclusion
Finally, porosity in welding can be a typical concern that impacts the quality of welds. By determining the typical root causes of porosity and applying best practices for prevention, such as appropriate welding methods and screening actions, welders can make certain top quality and reputable welds. It is necessary to focus on avoidance approaches to decrease the event of porosity and keep the integrity of bonded frameworks.